Continuous Improvement is very focused on reducing waste in a system.
A lot of the processes in a Continuous Improvement system are designed to find waste through Go See observations, determine how to reduce waste through root cause problem solving and then implement improvements to reduce waste.
But what exactly is waste ? How is it defined ? what does it mean ? and how do we recognise it ?
This blog will focus on ‘waste’, and how to identify and measure.
Waste – definition
Identifying opportunity is based on determining if activities are value add, value enabling or waste:
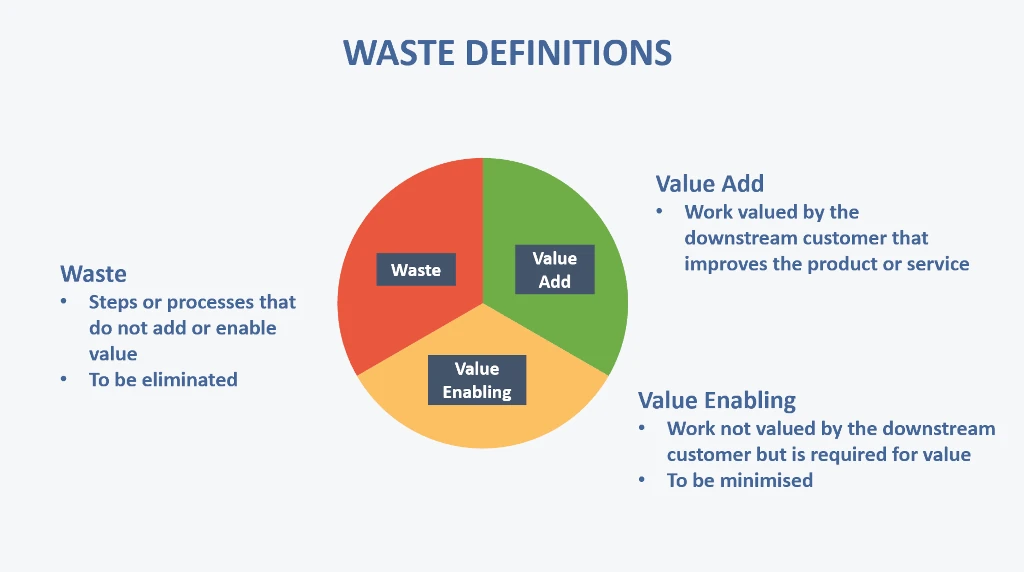
- Value add work is work directly valued by the downstream customer that receives the product or service. It’s any work that improves the product or service as defined by the customer
- Value enabling work, whilst not valued by the downstream customer, is required to actually do value add work. As such – this should be minimised.
- Waste consists of steps or processes that do not add or enable value. These steps can be reduced or eliminated altogether with no adverse impact on the product or service received by the customer
Waste – different types
Waste can take multiple forms and a useful acronym to remember when looking for waste is ‘WOODMITS’ – so called because collectively the 8 types of waste form the acronym ‘WOODMITS’:
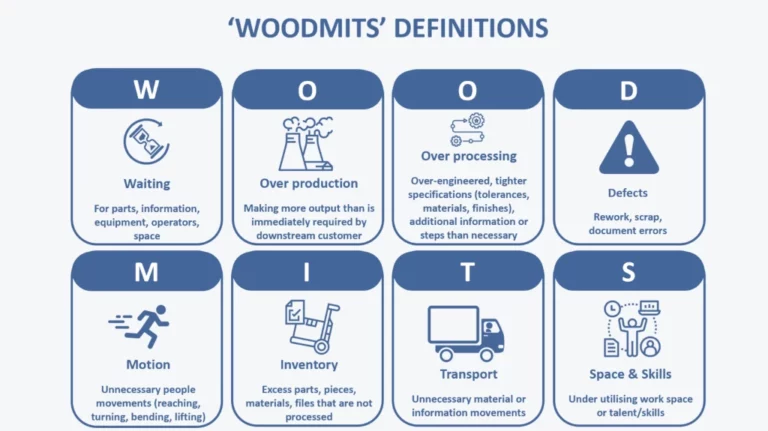
- Waiting – occurs frequently on the floor or in the field – with operators or staff waiting for parts, information, equipment, other operators or simply space in which to operate
- Over-production occurs when making more output than is immediately required by the downstream customer. This results in unwanted inventory
- Over-processing – effectively over-engineering or doing more work than needed can be hard to see – and requires working closely with the customer to really understand what they require – even going to see how the downstream customer uses the product or service so you’re aware of what the customer actually values
- Defects – these are more obvious and consists of rework (where you touch the product or service more than once), scrap or document errors
- Motion – where someone is having to reach, turn, bend or lift more than might be needed in a well engineered process. This might also include equipment making larger swing moves or linear moves than needed (for example assembly or pick and place robots)
- Inventory – again not always so easy to see – as you’re looking for excess inventory. Some might be easily visible – including ‘squirrel’ stores, old stock that hasn’t moved in years. Other excess inventory might not be so clearly visible. What could you get the inventory down to if the process flow was changed ?
- Transport – where materials are doing unnecessary additional moves or documents or files are taking additional work steps
- Space and skills – are existing work space and people’s talents and skills being fully utilised ? Are people working to the right level ?
Waste/loss frameworks
Finding waste can be difficult and non-intuitive but in some instances you can set-up waste or ‘loss’ frameworks that can calculate exactly how much waste there is in a system.
The Overall Equipment Effectiveness (OEE) is one such framework and is used when equipment is the main constraint to producing more output:
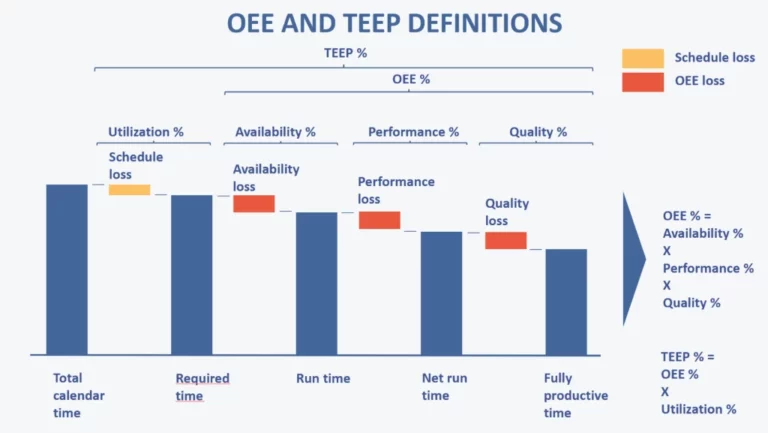
OEE can help you understand exactly how productive a system is (or conversely how much waste is present in the system). OEE is commonly defined as the product of Availability, Performance and Quality – and is calculated as a percentage – the higher the percentage then the better the OEE (and the lower the loss in the system).
OEE tells you how to increase production in an equipment centric process. Reducing any of the losses in the OEE framework will increase volume.
The benefits of a loss framework like OEE is that
- Waste is instantly measurable and gives everyone a common framework of where the losses are occurring and how much
- You can understand waste losses in real time
- The more granular you make the losses the better you can understand what to improve
- You can instantly see the resulting improved OEE whenever you make improvements that reduce waste
In some businesses, the process constraint is not equipment based but people based, in which case Overall Labour Effectiveness – OLE – can be used instead. This is likely the case in service industries such as backing or retail.
The OLE can be calculated in the same way as OEE ie as the product of Availability, Performance and Quality but these losses are calculated from the viewpoint of the operator rather than the equipment:
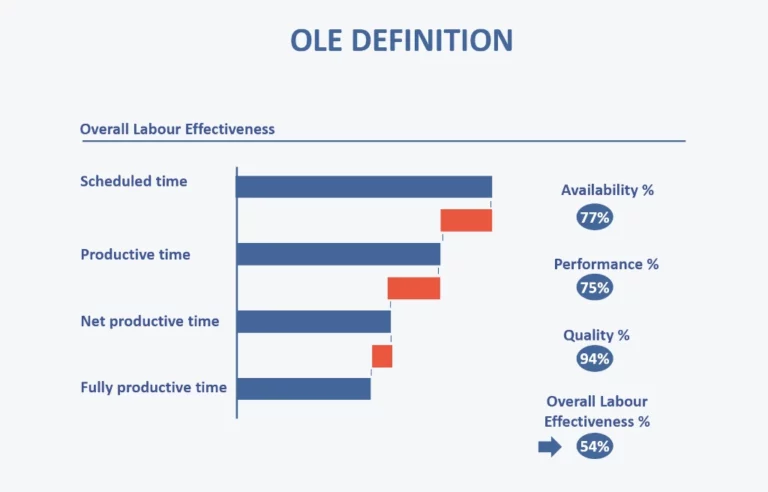
Read our waste/loss framework blog to understand more on both OEE and OLE and when and how to use each framework.
Summary
The main points covered include:
- What is waste: Waste consists of steps or processes that do not add or enable value as defined by the customer. Waste can be reduced or eliminated altogether with no adverse impact on the product or service received by the customer
- Different types of waste: 8 types of waste exist and WOODMITS is commonly used as an 8 letter acronym to remember them i.e., Waiting, Over-production, Over-processing, Defects, Motion, Inventory, Transport, Space and Skills
- Waste/loss frameworks: Overall Equipment Effectiveness (OEE) and Overall Labour Effectiveness (OLE) are examples of waste/loss frameworks that are commonly used in systems to measure the amount of waste in a system