Process confirmations – How to ensure that change sticks
Imagine you are pushing a ball uphill and want to stop the ball rolling down again. If you leave the ball it will roll down on its own and you’ll have to push it back up again. This is likely to be frustrating! a ‘chock’ comes to mind as the ideal means of holding the ball stationary.
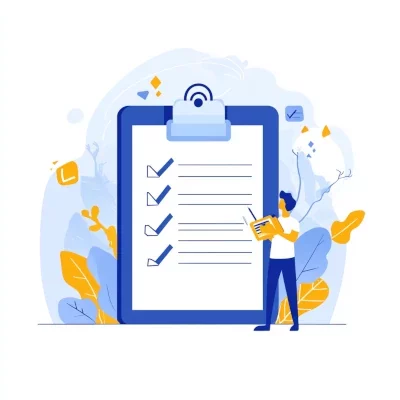
Similarly, making improvement can be thought of as rolling a ball uphill – either in big steps such as in major transformations or smaller incremental steps as in Continuous Improvement. A great mechanism to hold the ball in place (and stop the improvement from rolling back to where you started) is to use process confirmations. Process confirmations are designed as the ‘chocks’ to hold and lock in the improvement after each improvement change is made.
A ‘process confirmation’ is essentially going to the front line, observing the process, checking its following the expected and documented process and talking with the operators/staff.
This is your guide to process confirmations!
How they work
Process confirmations essentially check that the new process is actually being followed by staff and operators.
The process confirmation needs to be done in a structured way. Whilst ‘walking the floor’ is a fairly common way of understanding what is happening in an operation (and is very effective for quickly scanning all operational areas and also ensuring leadership visibility), we also recommend completing structured process confirmations as well.
Before they can be started, process confirmations require both that:
- the new process has been documented – ideally in a simple and readable format e.g., One Page Instruction sheet;
And,
- that operators have been briefed and trained, if needed, on the new process;
A process confirmation should use a structured template – with the key observational check points defined (which should match the process documentation).
During the process confirmation, a front line leader should check that the operator
- understands the new way of completing the process (and why this is the best way of completing the process)
- is following the expected process
- knows where to find the process documentation
It’s important to note that if the operator or staff is not following the new process, the leader should check why – it could be one of several reasons – each of which drive different follow-up actions. For example:
- Operator/staff does not know the process i.e., has not been briefed or trained or does not know where the documentation is
- Operator/staff has found a better way of completing the process – in which case the ‘standard’ way of completing the process needs to be updated accordingly
Actions
The process confirmation provides a great coaching opportunity for the frontline leader to talk through with staff/operators the correct way of completing a process. This kind of change is effectively immediately.
However, there may also be additional actions taken from the interaction that need to be implemented after completing the process confirmation e.g.,
- Conduct further training
- Revise the process documentation
- Conduct further problem solving to address issues identified by the operators/staff on the new process
Ideally, capture these actions immediately to ensure you don’t lose them.
How often should they occur ?
The frequency/schedule of the process confirmations should also be defined – so that front line leaders are regularly completing the process confirmations.
Process confirmations should be higher frequency immediately (e.g., daily/weekly) after the new process has been introduced. If process confirmations show that operators/staff are correctly following the new process then the frequency can be reduced (e.g., fortnightly/monthly).
The frequency will be dependent on how many operators are using the process, how often the crews change (is this a multi-shift/crew operation) and the complexity of the new process itself.
Tips to make them more effective
Some useful tips to consider when conducting process confirmations:
- Ensure you’re well prepared prior to the process confirmation. Make sure you have a copy of the process documentation beforehand and you’ve fully read through all the steps yourself (and it’s the same version the operator has). This process documentation should easily available and simple to understand – ideally in a One Page Instruction format (with supporting graphics).
- As a front line leader, its your responsibility to set the tone and effectiveness of the process confirmation and use the time as a coaching opportunity. Ensure that the operator/staff know prior to the observation the purpose of the process confirmation and what process is being observed.
- Ensure you capture and implement the improvement actions that come out from the observation. If you don’t action the improvement insights, you’ll simply see the same issues/opportunities the next time you complete the process confirmation. As a frontline leader it’s on you to improve the working conditions and processes.
- Try to establish a fixed schedule for completing the process confirmations and build into your regular routines (e.g., set hours on set days of the week). This is more likely to ensure the process confirmations actually happen.
- Ideally, try to use an online system to record the results and the actions that come out of the process confirmations. Use the system to ensure you and other leaders deliver on the actions.
Conclusion
Process confirmations may seem like hard work but
- a) they work; they are a tried and tested method
- b) you choose how much effort to put into them – both the frequency and time spent on them
- c) you choose which processes you want to process confirm – you should focus on the processes which are reasonably frequent and where there is current high variability in performance across operators and staff and the most impact achieved by reducing that variability
- d) similar to ‘walking the floor’ they provide additional benefits bringing you closer to the front line, providing a useful/structured coaching opportunity, and giving you visibility to the floor
Process confirmations are a great way to ‘lock in’ performance uplift, stopping the improvement ball from rolling back down the hill and achieving long term sustainable improvement!