Sustained improvement – how to sustain initiative performance uplift
Ensuring a new initiative ‘sticks’ is critical for sustained improvement.
As the improvement initiative is started and performance quickly improves, it’s tempting to immediately declare success and walk away!
However, rather than walk away, you need to look after the initiative to ensure it thrives, like a well watered plant, otherwise it will start to wither.
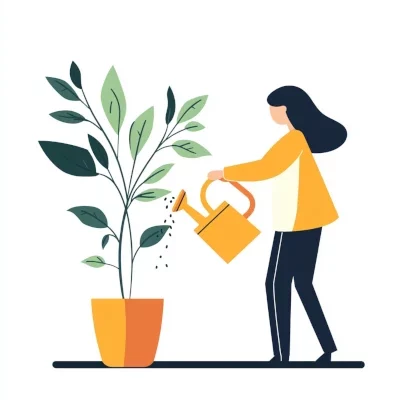
A likely outcome of assuming that a new improvement can now be treated as ‘Business-As-Usual’ too soon is that most, if not all, of the performance improvement will be lost.
The result is that performance will revert back over time to where you started – or close to it! Why does that happen and what to do about it ?
This guide aims to give you a good understanding of why its difficult to achieve sustained improvement and what to do about it.
Why initiative improvement can fade away
The core reason for this happening is that the new practices or processes have dropped away and the old behaviours have reasserted themselves – and operators and staff are back to the way they’ve always been doing it…
The reasons might vary – we’ve seen instances of:
- It might be easier to do the old way…
- Some operators and staff might not have been taught the new way when the improvement was implemented;
Or,
- There has been turnover in the area and the original team members have moved to other areas.
What we would like to happen, of course, is to see sustained improvement but this won’t happen for a process change without taking sustainability steps – and achieving ‘lock-in’ of the performance uplift.
Note that this issue is really specific to process improvements where people are being asked to change the way they do something. For some initiatives, like procurement supply switches or equipment changes (capex or engineering driven), the change is locked in as soon as the change is made. This makes these type of supply changes or equipment changes much easier to lock in sustained improvement.
Five key steps to achieving sustained improvement
Initiative sustainability should be addressed during all phases of an initiative to successfully achieve sustained improvement.
Sustainability work steps need to be thought about during implementation planning.
Five key sustainability steps that should potentially be planned for implementation are:
- Define processes and ensure the new way of working is documented
- Implement ‘error proofing’ if possible
- Brief, or train if needed, operators on the new way of working
- Ensure KPIs are tracking the effectiveness of the new process
- Set-up and start process confirmations – based on the new processes
Let’s discuss each of these in more detail.
1. Define processes and ensure the new way of working is documented
When process improvements are made or a new process set-up, making sure that the new process is well documented is a first key step in achieving sustained improvement.
Documentation is a critical step in ensuring operators/staff complete the process in a consistent and repeatable manner no matter who is completing the process. Without any documentation, the process will be completed inconsistently depending on who is completing the process and whatever they think is the best way of completing the task.
It’s difficult to standardise and maintain a new process without documenting the process. This documentation is needed for briefings, training and longer-term reference.
If the process is not documented anywhere, its unreasonable to expect operators or staff to follow new process steps.
Documentation is even more important in multi-shift operations where standard procedures are expected across multiple crews.
Documenting what the new process looks like requires agreement from all operators or staff about what is actually the best, standard way of completing the task – so just completing this step ensures that the people who actually do the work have had input and agree to the changes.
2. Implement 'error proofing'
Ideally, there is a way of ‘mistake-proofing’ or ‘error-proofing’ the new way of doing something.
Mistake-proofing, also known as Poka-Yoke, ensures sustained improvement as there is only one way of completing the task – the right way…
The concept of Poka-Yoke was first introduced by Dr. Shigeo Shingo in the 1960’s. The Japanese term “poka-yoke” is widely used – especially in lean and literally means avoiding (yokeru) mistakes (poka).
In mistake proofing, some asymmetry is introduced into the assembly or process to ensure that choice is taken out of the process and there is only viable way of completing the assembly of process.
Great examples of this are:
- Mobile phone ‘SIM’ cards which have one corner cut out so that they can only be used in the SIM receptor in a single way
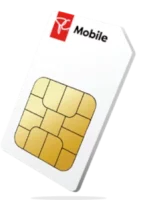
- Plugs – particularly with an ‘earth’ connection – are designed to be asymmetric preventing a user from incorrectly inserting the plug into the power outlet
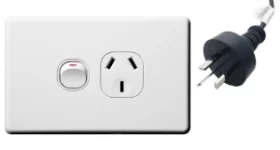
3. Brief, or train if needed, operators on the new way of working for sustained improvement
For simple changes (i.e., 10 minutes instruction) then a concise briefing is sufficient to get the key points of the new process across; for more involved process changes then a more involved training session is needed.
It’s unreasonable to expect staff or operators to complete a process in a new way without actually briefed or trained on the new way – and yet we’ve witnessed this multiple times…
A single briefing is likely insufficient; multiple briefings may be needed until all staff and operators across all crews ‘get it’ and fully understand what is required.
Try to make the briefing concise and visual. Use a ‘One Page Lesson’ sheet if you can – these are highly visual and easy to quickly understand and use as a reference. Post the One Page Lessons as close to the work front as possible.
The briefing also needs to make clear where the documentation for the new process can be accessed. Staff/operators need to be able to easily access the documentation for ongoing reference.
If the process is quite complex, then you may also need to run a specific training session on the new process.
Ensure that any training documentation is continuously updated and always up to date. New starters need to be trained on the new processes when starting in the area – otherwise any benefits will inevitably be lost due to staff turnover.
4. Ensure KPIs are tracking the effectiveness of the new process
The performance of the new process needs to be actively tracked through a mix of impact and process KPIs during implementation. Ensuring that these KPIs actually reach the expected targets for a multiple business cycles will help avoid declaring success too early and help achieve sustained improvement.
Whilst impact KPIs measure the output or benefit of the initiative (e.g., cost saving, productivity uplift) they are typically lagging KPIs measuring the end result. Process KPIs, on the other hand, are leading KPIs that can be used to directly see if the initiative’s input levers have improved.
If the KPIs fall away, then this should trigger root cause problem solving to define countermeasures needed.
Success should only be declared when results show sustained improvement over an extended time period – for example 8 to 12 weeks depending on the business cycles operating. There are no hard and fast business rules defining how long the KPIs should be tracked – just sufficiently long that the improvement team have confidence in sustaining the performance uplift.
5. Set-up and start process confirmations - based on the new processes
The final and ultimate way of ensuring sustained improvement is to regularly check the process is actually working as expected after completion – and if it’s not – then take appropriate action.
Process confirmations essentially check that the new process is actually being followed by staff and operators and helping to achieve sustained improvement.
The process confirmation needs to be done in a structured way. Whilst ‘walking the floor’ is a fairly common way of understanding what is happening in an operation, its more effective if structured process confirmations are completed during this time on the floor.
Process confirmations are a fairly structured review of the way the work is being done. They not only identify if the process is not being followed as expected but provide a great coaching opportunity with the frontline. The reviewer, the person completing the process observation, should ensure the operator is aware ahead of time of the process confirmation and the process confirmation will be done.
The process confirmation identifies if an operator understands the new process (and knows where the documentation is), observes the operator completing the process, confirms if the operator is following the steps defined in the documentation and, importantly, talks through the observation and findings in a discussion between the reviewer and the operator.
Learning should be two way and also a good opportunity for the reviewer to understand additional opportunities for improving the process.
Process confirmations are a whole subject in itself – and the subject of a longer post also available to you online.
Conclusion
‘Locking-in’ in sustained improvement is one of the hardest steps in implementation but these five steps will enable you to confidently implement processes that will support you in sustaining the uplift.
The five steps are not mutually exclusive and you will want to combine several of the approaches in a single initiative.
Read further for more information on achieving sustained improvement in your Improvement Program: