Successful always-on change capabilities
Ideally, your organization is capable of successfully making improvement happen anywhere in the organization whether its Continuous Improvement or major Transformation.
In this ideal world, your organization has Continuous Improvement programs happening throughout and is also able to implement major transformational changes when needed – responding quickly to external market conditions or internal changes as needed.
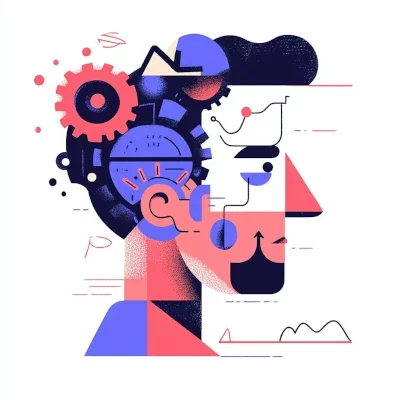
OK – back to reality… how to get there ?
To get to this stage, your organization needs:
- Always-on change processes used throughout the entire organisation
- Good change process disciplines
- Strong awareness and understanding by everyone of how these processes work
This post is a guide on what that entails and also provides a high level roadmap of how to get this capability.
Good change processes used consistently throughout the Organization
As detailed in our other posts, the key change/improvement processes that you want to successfully make change happen (either Continuous Improvement or Transformational change) are:
- Idea contribution
- Implementation planning
- Stage Gating
- Reporting
- Target setting
- Progress reviews
- Sustained improvement
We’ve talked in detail about what each of these are but how do you ensure the organization is capable of using these processes in the right way consistently in every area ?
Its likely you already have some of these processes, sort of working in some way, in some areas but that’s a long way from ensuring every area is running these processes the best way.
You may be using multiple spreadsheets to keep track of everything. This gets you some of the way but its not scalable, or easily replicable and not sustainable. Are there multiple spreadsheets ? Who has ownership over them and is maintaining them ? Can everyone access them ? Can you easily generate reports from them ? or is this another manual process ?
How do you control who sees what ? Or can everyone see everything ?
If you are using manual processes, who is telling people how to do these processes ? Is there any consistency at all ? Are people from one area of the company doing things completely differently from another area ?
Realistically to actually get these processes working consistently, everywhere, you need an online system that:
- Provides each of these processes:
- Idea contribution – add ideas, share with others, give feedback, convert to initiatives
- Implementation planning – define initiative work plans, allocate resources, define benefits, risks and issues
- Stage gating – ensure that all stakeholders see the information needed and control when initiatives pass each stage gate
- Reporting – generate multiple reports, charts and dashboards at any time
- Target setting – define targets by team (both top-down and bottom-up)
- Progress reviews – conduct progress reviews with KPIs, actions, risks and issues tracked
- Sustained improvement – track initiative KPIs and lock-in sustained improvement
- Ensures that everyone has access to each of these processes anytime they need
- Ensures that each person can see what they are entitled to see
Trying to do this without an online system would be virtually impossible and would require huge manual effort, would not scale across your organization, would involve too many people who would probably be Single Points of Dependency, would likely be inconsistent and processes would constantly fail to the point they would be deemed ineffective.
Fortunately, there are systems today that do all of this – and Lypta is one of them 😊.
Consistently disciplined change processes
Even with good systems in place to support your change processes, you still need good discipline to utilize these systems properly.
Common change process issues include:
- Initiative implementation: Not all work steps completed; KPIs have not reached the expected target levels
- Implementation planning: Initiatives don’t have all the required information (work plans are missing; measures of success are not explicit); sustainability steps are missing
- Progress reviews: Reviews don’t happen at all; scheduled start time constantly changes; reviews start late; key people are late or don’t attend
Allowing poor disciplines (low standards) on key change processes will take a toll on the effectiveness of these processes and ultimately lead to people saying the processes don’t work and then dropping the processes altogether as they’re ineffective.
This would be a mistake!
Ensuring good process disciplines exist, fall naturally on the Improvement team. However, this is impossible to fix without senior leadership support – so a first step in fixing change discipline is to enlist senior leadership support:
- First, make them aware of the issues and discuss with them how to approach these issues
- Second, ensure they lead from the front on these processes and
- Third, actively coach them when needed (to the point that they can then coach their teams as well).
This approach can be supplemented with using small process checks to ensure poor discipline is visually noticeable. Examples include:
- Attendance trackers (a sort of ‘name and shame’ approach) – red/green to denote if someone attended or not. Tracking tis week by week is quite effective to visibly show who are the repeat offenders. And, as a quick aside, attendance means that the person was there at the start (or within 2 minutes of start time)
- Process confirmations on the efficiency and effectiveness of progress reviews. This requires someone to manually review the meeting in real time and then give feedback on both the efficiency and effectiveness of the meeting; this is a great way of providing coaching to all the attendees in the progress reviews (e.g., what worked well, what didn’t and tips for improvement)
Strong awareness and understanding by everyone of how these processes work
Everyone in the organization should be aware of your improvement process work – so they will need some capability building to get these skills.
There are lots of ways of ensuring your people have the skills including:
- Face-face training including ‘bootcamp’ training: ideal to people through an intensive 2-5 day training course to get people up to speed at the start of a Transformation
- Online training: enable people to train themselves at their own speed and convenience
- Training documentation: allow people to see documentation whenever needed as reference material
- On going coaching: continuously coach people on best practices
Read our detailed post on capability building for more information on how best to do this in your organisation.
Managing both Continuous Improvement and major Transformations
Lastly, ideally, your organization should be able to handle both Continuous Improvement and major Transformations.
Major transformations might only happen every three or four years but last 6-18 months each time with each transformation having hundreds of initiatives concurrently – likely being managed by a Program Management Office and headed by a Chief Transformation Officer or Program Manager/Director.
Conversely, Continuous Improvement initiatives will be happening continuously throughout the organization – with each area running their own initiatives independently in the line (i.e., by Business Leaders) with support from the overall Continuous Improvement or Business Excellence/Improvement program.
Whilst these two types of improvement programs are wildly different in approach, objectives, timelines, impact, and who is running them there is also a lot of commonality in that the process and systems used can and should be the same. There may be small subtle differences between the two types of Improvement programs but the principles remain the same:
- Idea contribution – same
- Implementation planning – probably more detailed for a major transformation and bigger investments, resourcing required
- Stage gating – same principles of stage gating needed but you want an easier gating system for Continuous Improvement (as less investment/planning/effort needed for each initiative)
- Reporting – generally the same type of reports, charts and dashboards needed but the Continuous Improvement reporting will be simpler
- Target setting – high level top-down targets only needed for Continuous Improvement; bottom-up targets not needed as initiatives are running on separate timelines
- Progress reviews – same (but different participants with the Transformation progress reviews involving more stakeholders)
- Sustained improvement – same
If you’ve managed to:
- get everyone access to a system that will enable you to complete a transformation
- given everyone capability building on how these processes run
then you should be able to use the same system and processes to run Continuous Improvement – or vice versa.
And you’ll have achieved an ‘always-on capability’!
Conclusion
In summary, to have always-on change capability in your organization so that you are able to manage and implement both major Transformations and Continuous Improvement programs, then you need:
- Always-on change processes used throughout the entire organisation – the fastest, easiest, most reliable, consistent, scalable, sustainable way of having these processes in-house is to use an online system that gives you all of these processes
- Good change process disciplines – requires you and your senior leadership team to understand what good looks like and coach people towards those standards on an on-going basis
- Strong awareness and understanding by everyone of how these processes work – requires your organization to build the capabilities of your people. This can be supported by good online training and on-going coaching
Hopefully, as a Chief Transformation Office, Head of Improvement or Business Excellence or even just leading Business Improvement in your organization, you now understand what is needed and can undertake the steps needed to get there.
Read further for more information on the capabilities needed for ‘Always-on’ change capabilities:
- Empowered workforce
- The roles needed in an Improvement Program and what they each do
- Maintaining good change process disciplines in your Improvement Program